Emergency Repair of ESCC in SUS316L Equipment | Innovative Repair with Kanmeta Cold Spray
A test was conducted at a petrochemical plant to evaluate cold spray technology for the repair of external stress corrosion cracking (ESCC) in SS316L equipment.
Before
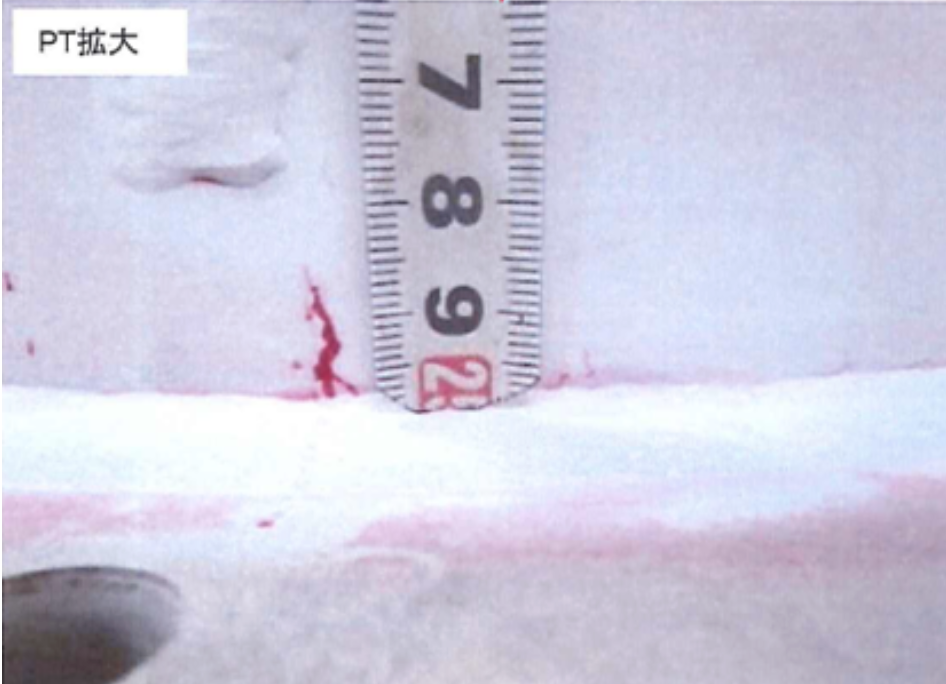
After
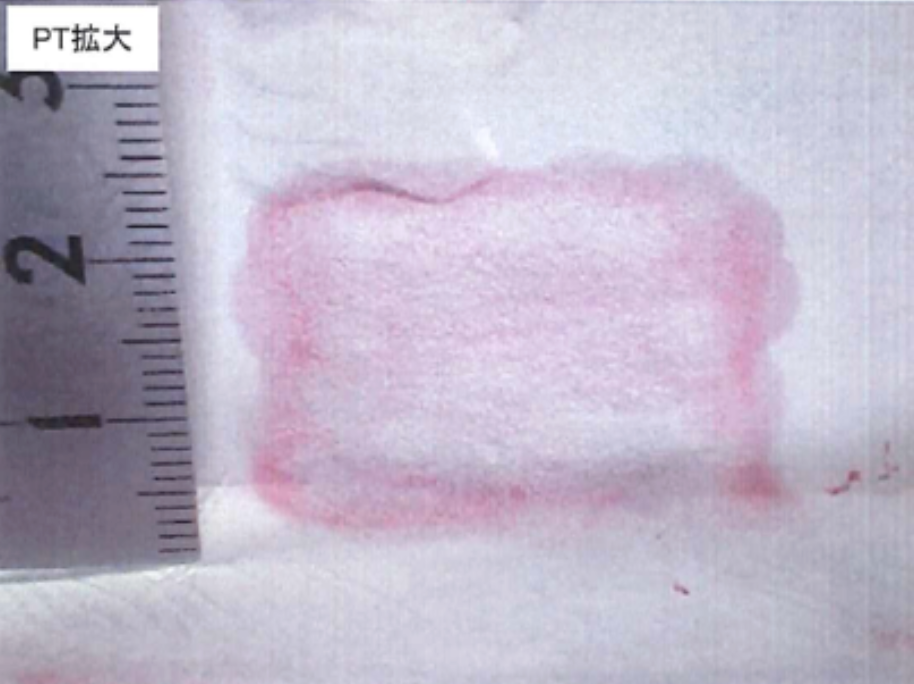
Customer's Challenge:
There are several concerns with conventional repair techniques for cracks and material loss in SS316L equipment:
1.High heat input from welding carries the risk of causing sensitization and further damage to the base material.
2.The base material is already severely degraded, and the heat from welding could propagate additional cracking.
3.Anti-corrosion thermal spraying may not be suitable in certain environments.
4.If thinning has already occurred, thermal spraying cannot adequately restore the material thickness.
Kanmeta Engineering's Proposal:
Kanmeta Cold Spray was chosen for the following reasons:
1.No high heat input, avoiding damage like sensitization to the base material.
2.No restrictions on coating thickness, providing excellent environmental barrier capabilities even in harsh corrosion conditions.
3.Flexible application makes it suitable for repairs on existing equipment.
Results:
1)A third-party inspection company confirmed the effectiveness of the cold spray as a sealing (patching) treatment for ESCC cracks.
2)Remaining internal cracks can be monitored regularly using external ultrasonic testing (UT).
3)Cracks were successfully sealed with a thick, high-environmental-barrier cold spray coating.
4)The cold spray was applied without causing any adverse effects to the stainless steel, even with concerns about heat damage.
5)The high-performance coating applied over existing equipment eliminates the need for equipment replacement through regular inspection and periodic maintenance.
Discover our advanced cold spray solutions for managing ESCC and enhancing the durability of your equipment.