Preventing Powder Build-Up Inside Large Stainless Steel Hoppers|Premium Fine Peening (PFP)
At a petrochemical plant, PFP treatment was applied on-site to prevent powder adherence (bridging and blockage) inside large stainless steel (SUS) hoppers.
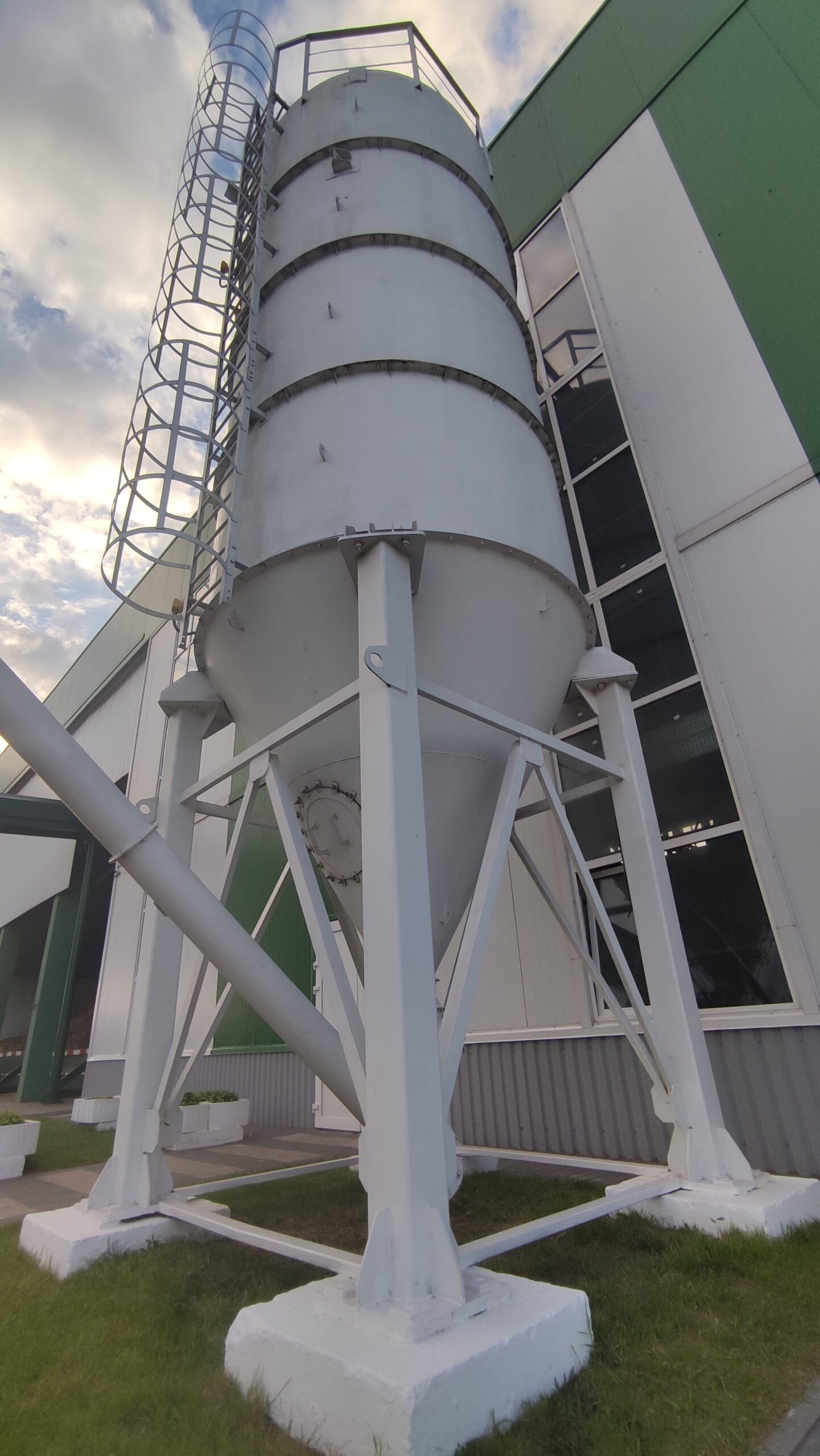
Customer's Challenge
The customer faced significant powder build-up (bridging and blockage) inside the hopper, impacting flowability. To improve powder flow, they used knockers and vibrators, but the vibrations caused damage to the hopper.
The Production environment did not allow for any foreign matter contamination, so applying coatings that risked contamination was not an option. Even buff polishing left traces of abrasive materials, leading to impurities being detected. Additionally, due to the large size of the equipment, on-site treatment was essential as removal was not practical.
Kanmeta Engineering's Solution
PFP treatment was selected for the following advantages:
On-Site Expertise: Leveraging our extensive on-site experience, we successfully performed treatment on large equipment without issues.
No Coatings: As no coatings were used, there was no risk of contamination.
Proven Effectiveness: Pre-release testing using sample powder (provided free of charge) verified effectiveness and enabled smooth internal approval.
Innovative Design: The textured surface minimized powder contact, reducing build-up.
Results
By improving powder flowability, we reduced the reliance on knockers and vibrators, preventing equipment damage
(replacement costs were previously in the tens of millions of yen annually due to direct, indirect, and opportunity loss costs).
✔Production efficiency increased significantly, contributing to major cost reductions.
✔We received positive feedback from the client, who noted, “The performance remains outstanding even after 5 years.” As a result, the solution was extended to equipment in other divisions.