Build-up and Crack Repair for Castings|Innovative Repair with Kanmeta Cold Spray
Cold spray was applied as a build-up and crack repair solution for cast ejector equipment in a petrochemical plant.
Before
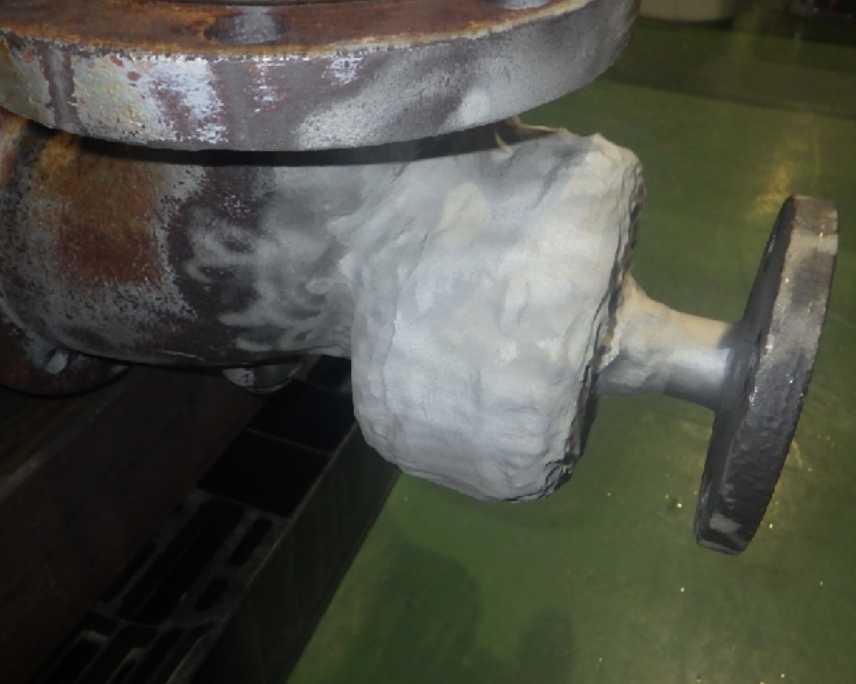
After
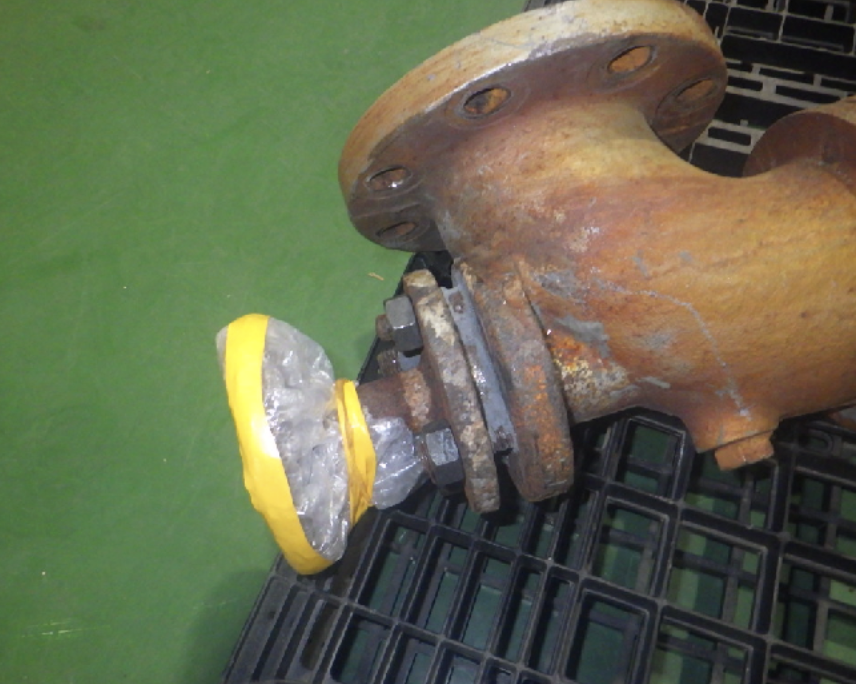
Customer’s Challenge
The customer had long struggled with the lack of effective repair methods for cracks and leaks in cast equipment. In this case, liquid leakage was occurring between the flanges, and while they used Teflon sheets as a temporary fix, it could not completely stop the leakage.
Existing repair technologies like welding and thermal spraying were not viable for the following reasons:
High Heat Input: Welding or other high-heat methods could damage the cast material (cast iron).
Thermal Spraying Limitations: Thermal spraying had a limited coating thickness and could not provide the necessary environmental sealing to stop the leakage.
Kanmeta Engineering’s Proposal
Kanmeta Cold Spray was selected for the following advantages:
No High Heat Input: Avoids damaging the base material, ensuring no harm to the casting.
Unlimited Coating Thickness: Provides sufficient sealing capability to block the leakage.
Flexible Application: Can be applied directly to existing equipment, allowing for easy adaptation.
Results
✔ The cold spray coating, with its high environmental sealing ability, effectively sealed the leakage between the upper and lower flange gaps.
✔ The cold spray was applied without any crack propagation, even to castings that were at risk of thermal damage.
✔ The existing equipment was covered with a high-performance coating, eliminating the need for part replacement.
Discover our innovative cold spray solutions for cost-effective and reliable repairs that save time and resources.