Industry-Leading Corrosion Protection
Excellence in Thermal Spray Technology
With over 50 years of experience as pioneers in protective thermal spray coatings for refineries and petrochemical plants, we've developed unparalleled expertise in the field.
Our proven track record includes installations at virtually every major refinery and petrochemical facility in Japan, with more than 10,000 successful applications completed to date.
Applications & Benefits
Corrosion Protection & Metal Loss Prevention
Enhanced Wear Resistance
Special Surface Properties (Non-stick, Release Coating & More)
Key Facts & Figures
Over 12,000 Installations Completed
Operations in 7 Countries Worldwide
250+ Coating Materials Available
70+ Years of Industry Experience
Introduction to Thermal Spray Technology
Performance Characteristics
Thermal spray coating, as defined by JIS H 8200:2006, is a surface treatment process where coating materials are heated to a molten or semi-molten state using combustion or electrical energy, then sprayed onto a prepared substrate to form a protective coating. The process involves two key steps, as suggested by the term "thermal spray": first, the coating material is "thermally" melted, then "sprayed" onto a properly prepared substrate surface.
During application, the coating material is heated by a heat source until it becomes molten or semi-molten. These heated particles are then atomized and propelled by compressed air toward the substrate. Upon impact, the particles flatten and rapidly solidify on the pretreated surface. The coating is built up through multiple layers of these overlapping particles.
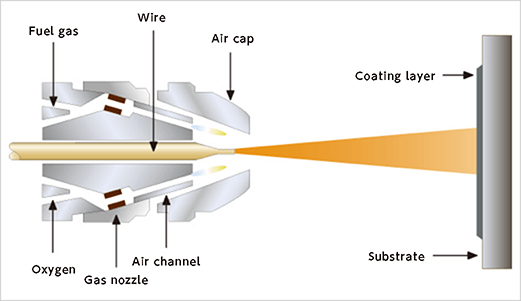
Why Choose KANMETA's Anti-Corrosion Coating Solutions
Custom-Engineered Coating Specifications
Drawing on over 70 years of comprehensive data and ongoing research, we develop tailored coating solutions backed by years of real-world performance testing.
Whether you're uncertain about material selection or seeking optimal corrosion protection strategies, our experts can guide you from the initial material choice through implementation.
We don't rely on guesswork – every specification we recommend is supported by proven results and engineered for your specific application.
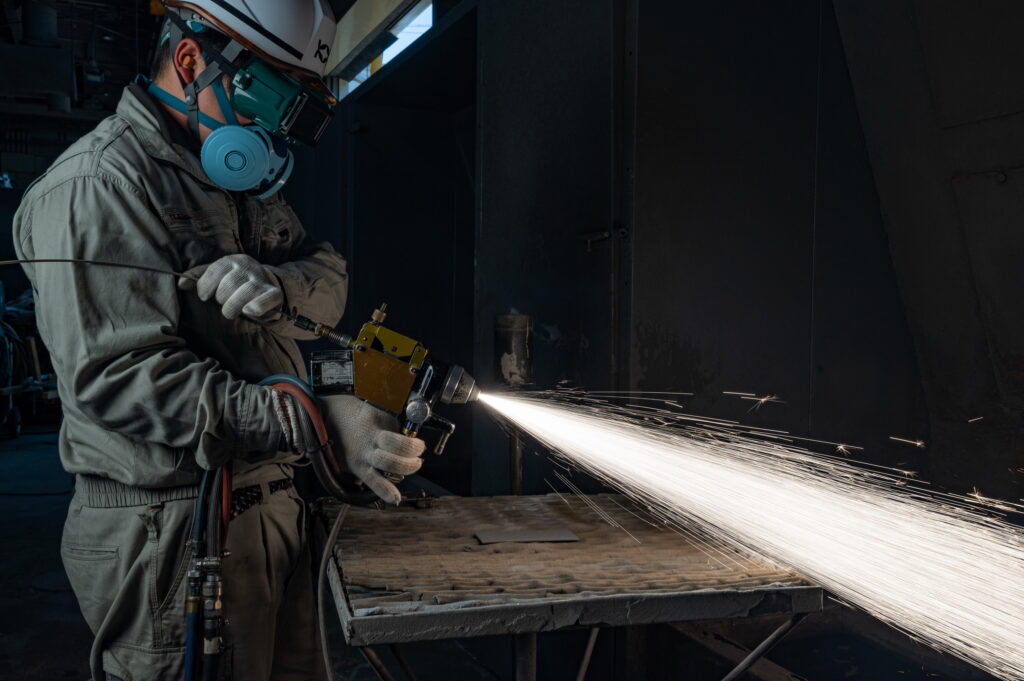
Seven decades of field-proven experience
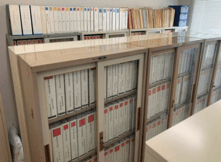
Portfolio of 250+ coating materials
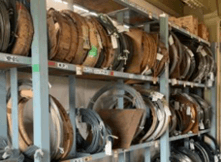
State-of-the-art research capabilities
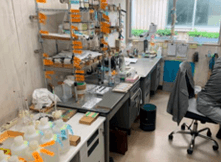
Extended field testing on operational equipment
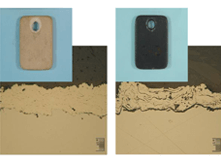
Emergency Response Capability
When urgent corrosion issues arise with tight operational deadlines, our rapid response team is ready to mobilize immediately.
With our in-house technicians and comprehensive inventory on standby, we can quickly assess and address your emergency coating needs, drawing on over 70 years of field experience. Count on us for fast, reliable solutions when time is critical.
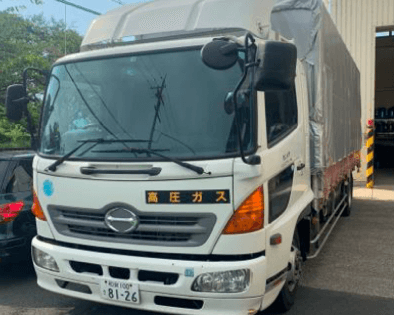
Comprehensive Maintenance & Inspection Services
In the aggressive corrosive environments of refineries and petrochemical plants, where conditions far exceed natural atmospheric corrosion, regular coating inspection is crucial for long-term performance.
At KANMETA ENGINEERING, our commitment extends beyond initial application to include comprehensive post-installation support. Our inspection teams conduct regular performance evaluations and detailed condition assessments to validate coating effectiveness and identify potential issues before they develop. Based on these thorough inspections, we provide detailed reports of our findings and, when opportunities for improvement exist, develop enhanced coating specifications backed by laboratory testing.
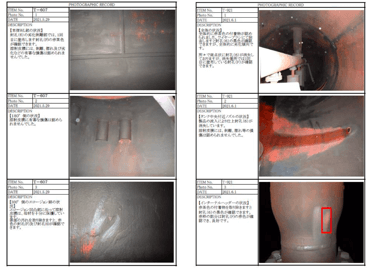
Trust Your Corrosion Protection Needs to KANMETA
ENGINEERING
The success of any coating system depends not only on perfect application but also on selecting materials that can withstand your specific operating environment. Our comprehensive approach begins with understanding your needs, followed by thorough material testing and analysis. This enables us to recommend the optimal coating solution for each piece of equipment.
Experiencing corrosion challenges with your industrial equipment? Let KANMETA ENGINEERING's expertise work for you – contact us today to discuss your corrosion protection requirements.
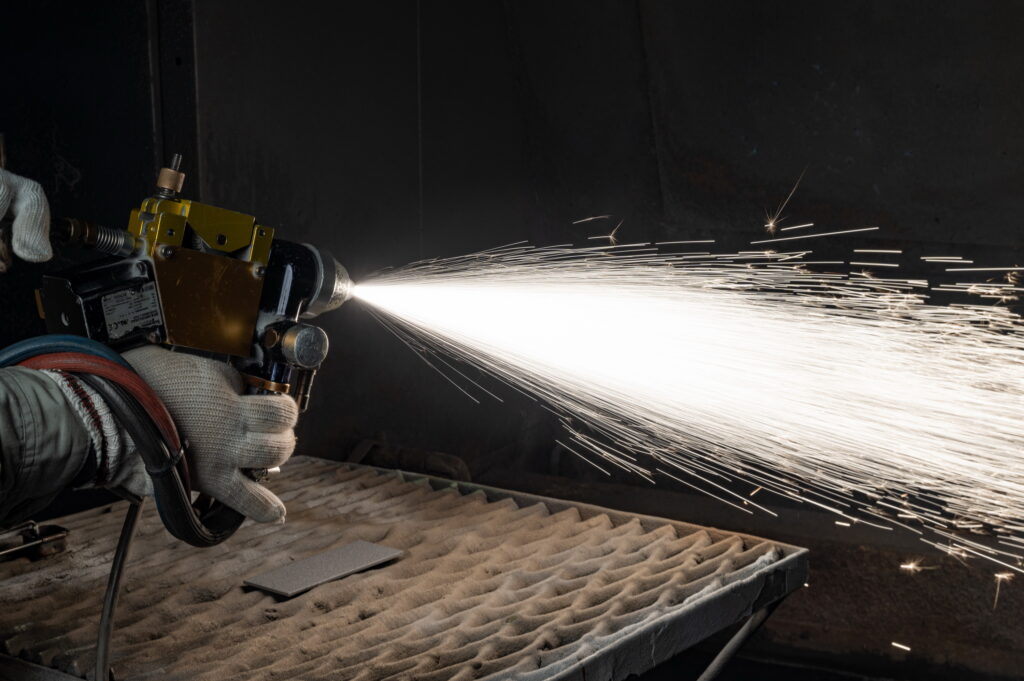